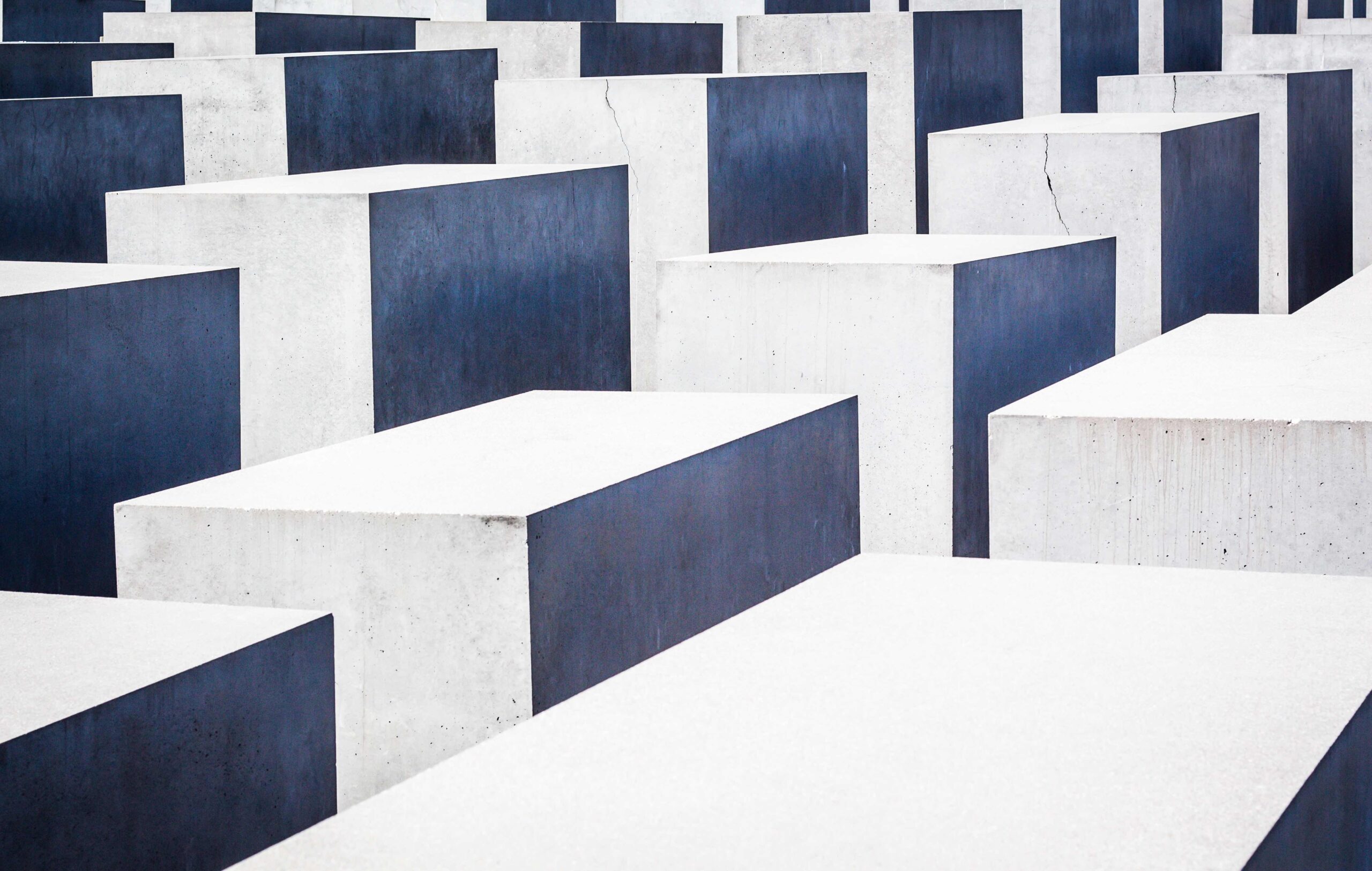
Design from the Ground Up, Unit First to Increase Your Return on Track and on Schedule
May 21, 2021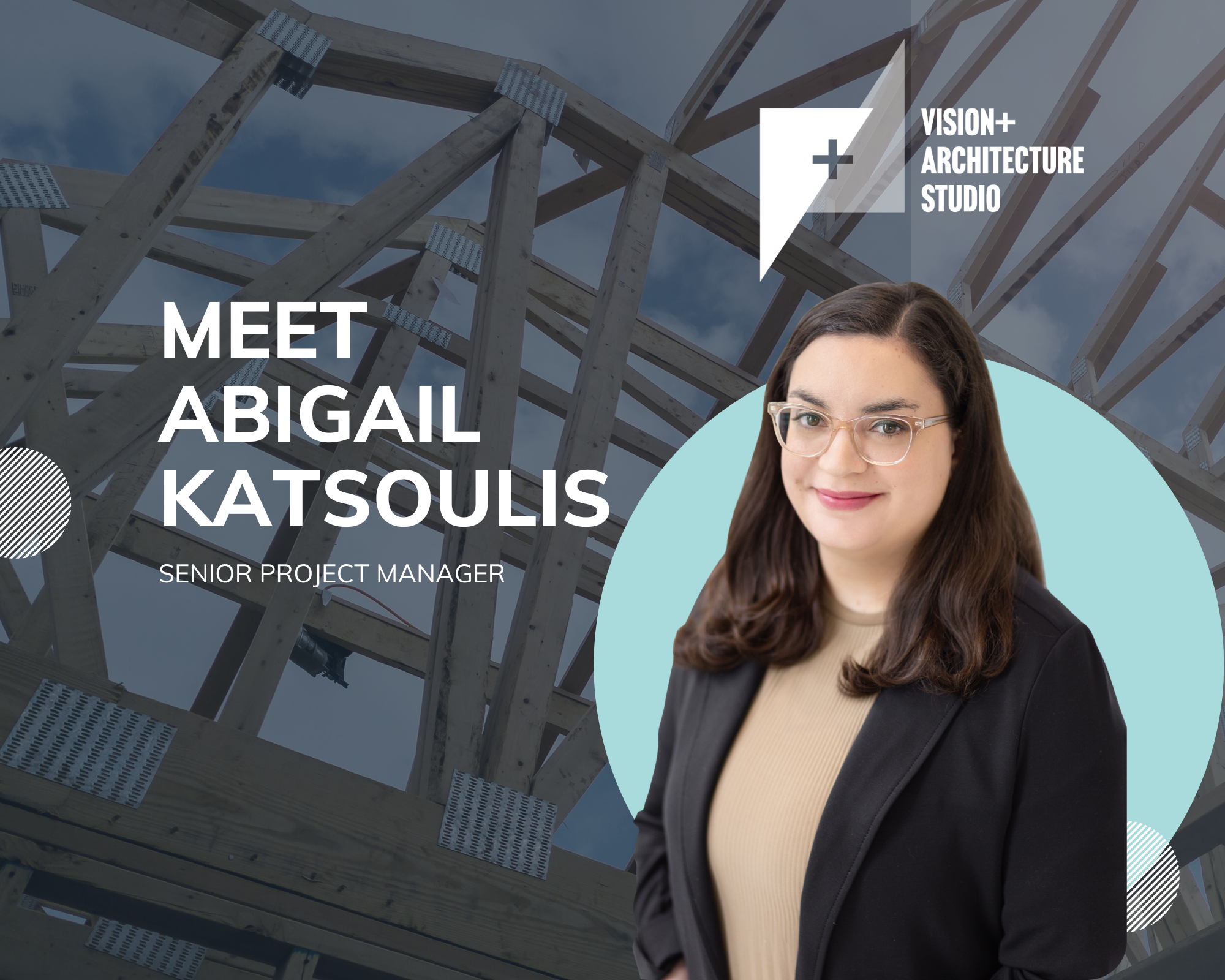
Meet Abigail Katsoulis, Vision+Architecture Senior Project Manager
June 1, 2022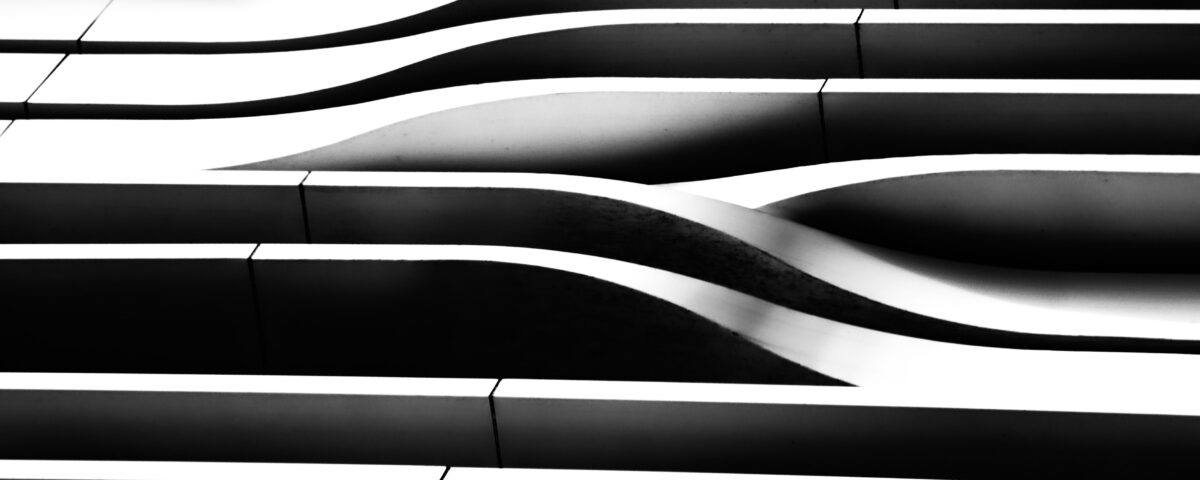
By Kevin Wallace, Architect and Development Adviser, Vision+Architecture Studio
With commodity shortages rippling across the United States economy as a result of the global pandemic – and threats of tariffs before that – the scarcity of supplies and the price increases they are causing are having very real effects on industry, including construction. In the housing and multifamily construction industries especially, the price of lumber has almost tripled in the last year, driving contractors to consider other, higher-quality materials such as CFS (cold-formed steel) framing, that are now much more affordable than the industry-standard wood. In markets where builders are already struggling to keep up with demand and housing inventories are incredibly low, exorbitant lumber prices present just one more hurdle – layered onto shortage of skilled labor and compressed timelines – to completing projects. Developers are looking for solutions to help decrease the cost of construction, speed up the schedule to turn buildings over much faster, and mitigate financial risk.
I recently sat down with Stephen Bezner, CEO of Texas Steel Tech, to talk about the new steel hybrid construction method he’s developed to help the multifamily construction industry stay on schedule and on budget for project completion throughout North Texas.
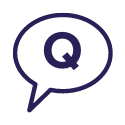
Most 3- to 4-story multifamily buildings are constructed with wood frames, and until recently that’s been fairly cost-efficient. Why hasn’t steel framing been more widely used in the industry?
Steve: Typically, hospitality and other mid-rise commercial buildings use a non-combustible frame system utilizing steel. Multifamily apartments usually stay under 3-4 stories because they can still be built using a combustible wood frame. The biggest issue was when you changed from wood to steel, you’d see an increase in the intangible costs such as design costs associated with building with steel versus wood. When you’re building with wood, even though your engineer does lay out the ground rules in the drawing set, a lot of it is prescriptive, which means your “engineer” is basically the carpenter working out of his truck, measuring, cutting and “engineering” your building with rules-of-thumb as he frames the building. He is following some prescriptive paths, but for the most part the city is relying on what he does for their inspection.
When you use steel, your engineer is offsite and they’re looking at your building as a standalone structure and calculating the frames to exact measure to be assembled in a factory before they’re delivered to the building site for installation. This cost of engineering was always about 3-5% more than wood, and it just didn’t make much financial sense when trying to pencil in your rental rates and preparing your property to sell. Almost every developer building apartments follows the same path of budget, entitlement, design and construction, lease up, and then selling the development to institutional investors to hold long term. Hospitality developers by contrast are more long term, because in most cases the developers also hold and manage their hotels as long-term investments and may keep them in their portfolio thirty plus years.
Until recently, when lumber prices shot up, steel didn’t really make sense for multifamily, which tend to go with the least expensive options during construction. We wanted to come up with something that wasn’t a true non-combustible but got as close as we could to non-combustibility while still being built similar to what the trades and contractors are used to in Type V multifamily construction.
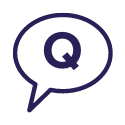
So, let’s talk about the typical multifamily construction process. What does the hybrid system you created replace during the framing process?
Most apartments are built with wood frame walls at 12- to 16-inch centers, with double top plate wood studs. Floor systems are built with either a TJI or wood truss floor system with plywood sheathing topped with a gypsum slurry or some type of lightweight concrete. When you’re framing with steel the expense that wasn’t making steel competitive with wood wasn’t our framing product, it was our typical non-combustible floor system. Typically, with CFS framing the floor system is 4 inches of concrete on a metal deck at approximately $5 to $6 per square foot. The metal deck floor system is about the same cost per square foot as plywood. So that wasn’t the issue. The issue is the $4-5 a square foot of concrete on top of the metal deck. We eliminate the cost of the concrete floor by marrying the typical wood frame floor system of plywood and lightweight concrete with our metal wall and joist system, giving us an acceptable “combustible” plywood floor system that we call our hybrid system.
We use a tongue and groove plywood floor, then put the gypsum on, which is exactly what contractors are used to in wood framing. There was no difference there. In wood, they would come back and pump a real thin concrete (with a consistency like syrup), and it’s a floating system that floats the floor level on top of plywood. They’re pouring against a wood bottom plate, the pour stop. With ours we just extend our track up, so our bottom track against our steel studs just becomes your pour stop.
The other issue we have is when we’re building a hotel, you build the first floor and have to finish the entire first floor, you put your metal decking down, your pour stops, and you have to wait for another contractor like your concrete contractor to come in and pour the concrete. You have to interrupt framing for a week to two weeks because the concrete has to prove up, it has to cure. That means we’re off the job for a week or two and we can’t put our walls up because the walls sit on top of the concrete. With a wood deck, you can start pouring the next level while framing right on top of the plywood so there’s no stoppage in moving forward, that’s a good thing. We’ve now also saved around $4-5 per square foot on concrete costs. An additional benefit is the load and weight of that concrete, we used to satisfy that with heavier steel studs. Now we’ve been able to reduce the gauge of the steel studs of the building down because we don’t need to have the higher gauge load capacity to carry what is now a significantly lighter weight structure. With concrete, you’re talking 60-70 pounds per square foot, where your plywood is probably 3-4 pounds per square foot. It’s a big difference.
We’ve been able to trim the budget by the contractor not having to pour concrete, and we also get to speed up the operation, because once we do our first-floor walls, we drop our steel hybrid floor trusses into place, and we deck it all as we progress through the building. As we get to the far diagonal corner, we’ve already floor decked the whole building and our next walls are already going up to the next floor. We’re able to process through the whole building quicker. There’s no stoppage with the system.
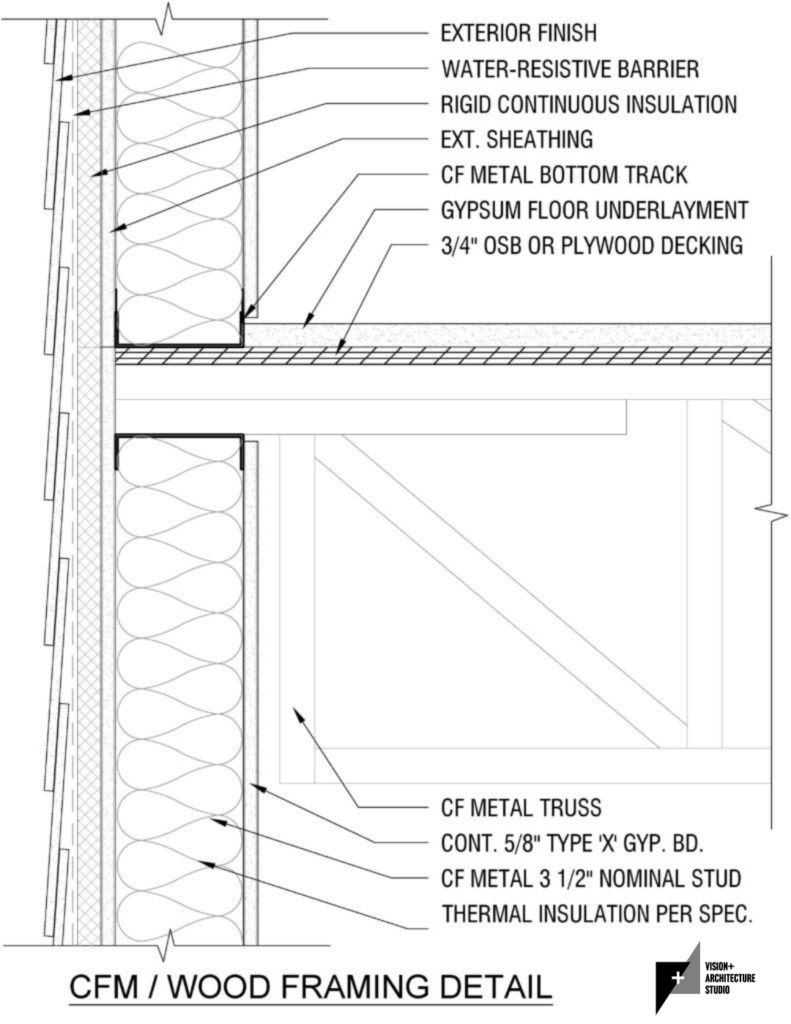
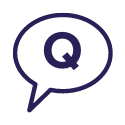
One of the holdups of using steel is that multifamily construction laborers aren’t as familiar with installing it as wood. Is the hybrid system familiar to those installing it on site? What are the benefits of building with steel?
Our UL assemblies match what has existed for many years. There’s really nothing new about it, we just call it hybrid because we introduce a wood product into the system.
Anyone building apartments is going to be risk averse because if their cost basis goes up even a couple dollars a square foot, they’re going to take that hit when they sell that apartment. It really comes down to whether they’re willing to pay $2 a square foot more for a better product in steel. If it’s a long-term hold like a hotel, then longevity, low-cost of maintenance, and lower insurance rates are important.
Steel has so many other considerations and long-term benefits: insurance is lower, the lifespan of the building is much longer, you don’t have to treat for termites or mold, there’s a low cost of maintenance, and there’s very little trash on site because it’s all recycled at the factory.
Until now, most apartment builders would say they weren’t willing to pay that extra dollar or so a foot just to know that it was getting built in a quality fashion, it has to take the right developer to say that. Right now, we get a least a request every day for an apartment complex to transfer to steel. We’ve never had that, and it’s driven by timber cost and availability. That is the catalyst that let us present our case and create the hybrid system.
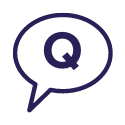
What are some aspects for steel and the hybrid system that multifamily general contractors might want to take into consideration?
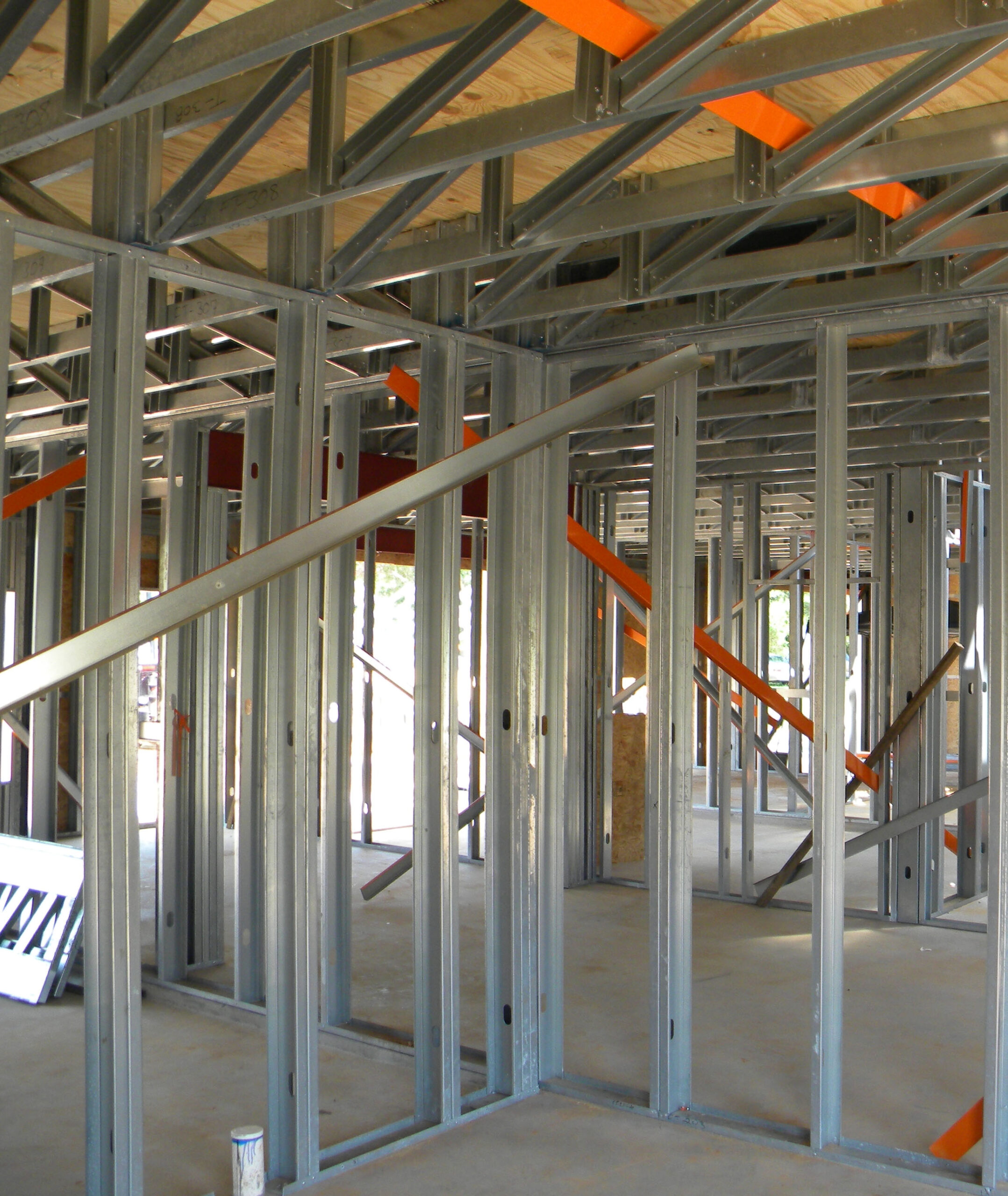
You can still sheath the exterior of the building with a wood sheathing or T-Ply product. You are required, however, to boost the exterior insulation because of the metal framing. This is required by the energy codes. Though some jurisdictions will remove it, the energy code mandates a complete exterior envelope insulation system or continuous insulation, CI. CI is not required with a wood frame.
A significant advantage of the hybrid system is that it falls within the Type V building code versus Type II code. Typically, once you get to light-gauge steel construction you’re kicked up to a Type II building code, which is more constrictive in your fire ratings and design criteria. The hybrid system provides most of the benefits of non-combustible construction but still Type V construction, so we stay in the lower requirements of the building code because we’re in Type V.
There may be a bit of a learning curve for electricians working on multifamily construction who are more familiar with wiring a lumber frame building, or the general contractor may have to expand their network to hire subcontractors who are familiar with it. If you have an apartment developer or general contractor and he has built with wood his whole career, he naturally wants to call on his electrician, his go-to guys, and they say, ‘we’ve never done a commercial building.’ The guys that have done commercial buildings have no problem with it because they don’t even want to touch a wood building. With wood framing the electrician has to drill holes, run Romex through small holes and tight areas, and have a guy up on top pulling it. When you’re working with steel the holes for wiring are already pre-punched, so you can use a shielded Romex or Romex with grommets and wire the building in half the time. The first thing the contractor should do is get the right subcontractors for the job to ensure it’s done properly and they’re not charging a premium because it’s something they’re unfamiliar with. Your labor should be the same, maybe less than with wood actually. And using steel doesn’t mean you have to contract the big commercial subcontractors either. You’re simply stepping up to a more mid-tier company that’s doing commercial jobs, mixed-use and hospitality.
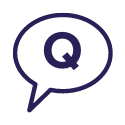
The three things a general contractor is concerned with when building a multifamily project are the cost of construction, the speed of construction, and financial risk. We know the spike in lumber prices is affecting all three, but how does steel alleviate those concerns?
Originally the problem was that the construction was just too foreign to begin with in terms of how it all went together, the flowing with the concrete and engineering. Take that out of the way, the solution is that in creating this hybrid structure/approach, you’re able to take the best of a steel structure, in terms of long-term panels, ratings, etc., and get the building up on time. Basically, the floor system’s construction is going to feel similar to the people doing the work on site, similar to timber construction, but overall, how they do that is much more analogous to what they’re used to. One of the other reasons they haven’t typically gone with steel was because of the stoppage in construction, and this new approach allows for continuous construction over the structure. The hybrid system wipes out a lot of those risk considerations.
I’ve seen movement on apartments to steel for the last 15 years, but they just wouldn’t make that $2 per square foot hurdle. They’re so used to not pouring concrete on second levels, that was always the issue. Now they don’t have to do that, the financial risk is lower and often more cost efficient than the old way of doing things with lumber. Also, there are more people who understand steel framing than there were 15 years ago, there’s more consistency in pricing of steel than wood, and there’s a lot more UL listed assemblies now than we had 15 years ago. There’s a lot of technical aspects that have improved along with it and made the entire process more efficient and affordable. Even products for the electrician, with pop-in grommets and shielded Romex that are much more readily available. When I started 25 years ago no one knew what a pop-in grommet was.
Essentially, steel and this hybrid system have far more benefits than wood, aside from the cost now, and the building quality and lifespan is much higher. When you can get all that for the same cost and then turn a higher profit in a few years when you sell the property because the building is higher quality, the decision is easy.